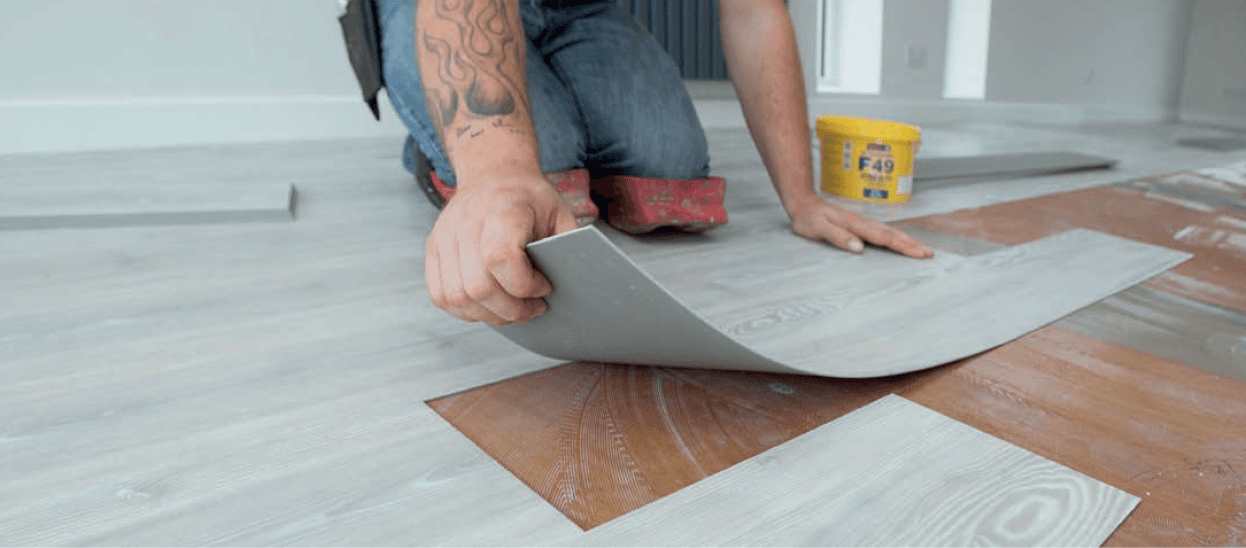
Luxury Vinyl Tiles (LVT): Complete Installation Guide for Flawless Finish
Core Requirements
LVT installations demand careful attention to detail according to BS 8203:2017:
- Sound subfloor preparation
- Proper moisture management
- Appropriate product selection
- Professional installation techniques
- Quality finishing procedures
Installation Process
Subfloor Preparation
- Mechanical removal of laitance
- Elimination of surface contaminants
- Thorough soundness check
- Smoothness assessment
- Basic preparation principles
- British Standards compliance
Moisture Management
- Mandatory moisture testing
- Calibrated hygrometer use
- RH level assessment (max 75%)
- Waterproof membrane application:
- Single coat for up to 98% RH
- Three-hour cure time
- Complete moisture isolation
- Prevention of floor failure
Key Components
Priming Solutions
- Essential surface preparation
- Optimized compound performance
- Absorbent subfloor treatment
- Time-saving options available
- Specialized applications:
- General-purpose primers
- Non-absorbent surface primers
- Calcium sulphate screed primers
Smoothing Compounds
- Perfect level surface creation
- Visual appearance assurance
- Heavy-duty options available:
- High compressive strength
- Excellent self-smoothing
- Heavy load capability
- High traffic tolerance
Flexible Solutions
- Plywood subfloor applications
- Steel surface installations
- Movement accommodation
- Crack prevention measures
- Appearance preservation
Technical Specifications
| Feature | Requirement | |---------|-------------| | RH Level Limit | 75% standard, 98% with membrane | | Cure Time | 3 hours for membrane | | Coverage | Varies by product | | Standards | BS 8203:2017 compliant | | Surface Types | Concrete, plywood, steel | | Traffic Rating | Heavy-duty available |
Installation Techniques
Adhesive Application
- Pressure-sensitive solutions
- Instant grab properties
- Pattern creation capability
- Proper roller techniques:
- Paint roller application
- Ridge flattening
- Trowel mark prevention
- Visual appearance protection
Quality Control
- Compatibility verification
- Manufacturer guidelines
- RAG consultation
- Over 5,000 floorcoverings
- 200+ manufacturer coverage
Common Challenges
Moisture Issues
- Leading cause of floor failure
- Residual construction moisture
- Rising damp problems
- Adhesive degradation
- Surface blistering
- Installation lifting
Prevention Measures
- Proper moisture testing
- Appropriate membrane use
- Correct primer selection
- Quality compound application
- Professional installation
Best Practices
Professional Requirements
- Standard compliance
- Proper tool selection
- Correct product application
- Quality control measures
- Regular assessment
Material Selection
- Appropriate primer choice
- Suitable compound selection
- Compatible adhesive use
- Quality control checks
- Manufacturer guidance
Long-term Benefits
Performance Advantages
- Extended installation life
- Maintained appearance
- Structural integrity
- Traffic resistance
- Load bearing capacity
Cost Efficiency
- Reduced maintenance
- Prevented callbacks
- Minimized repairs
- Extended longevity
- Customer satisfaction
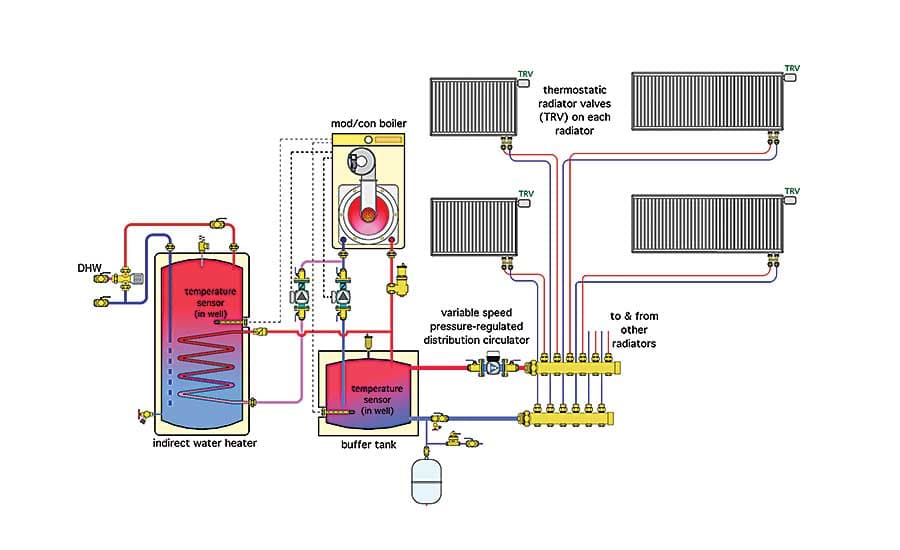
Hydronic Heating: A Solution for Net Zero Buildings
Explore how hydronic-based heating systems provide efficient solutions for net zero buildings while maintaining superior comfort levels.
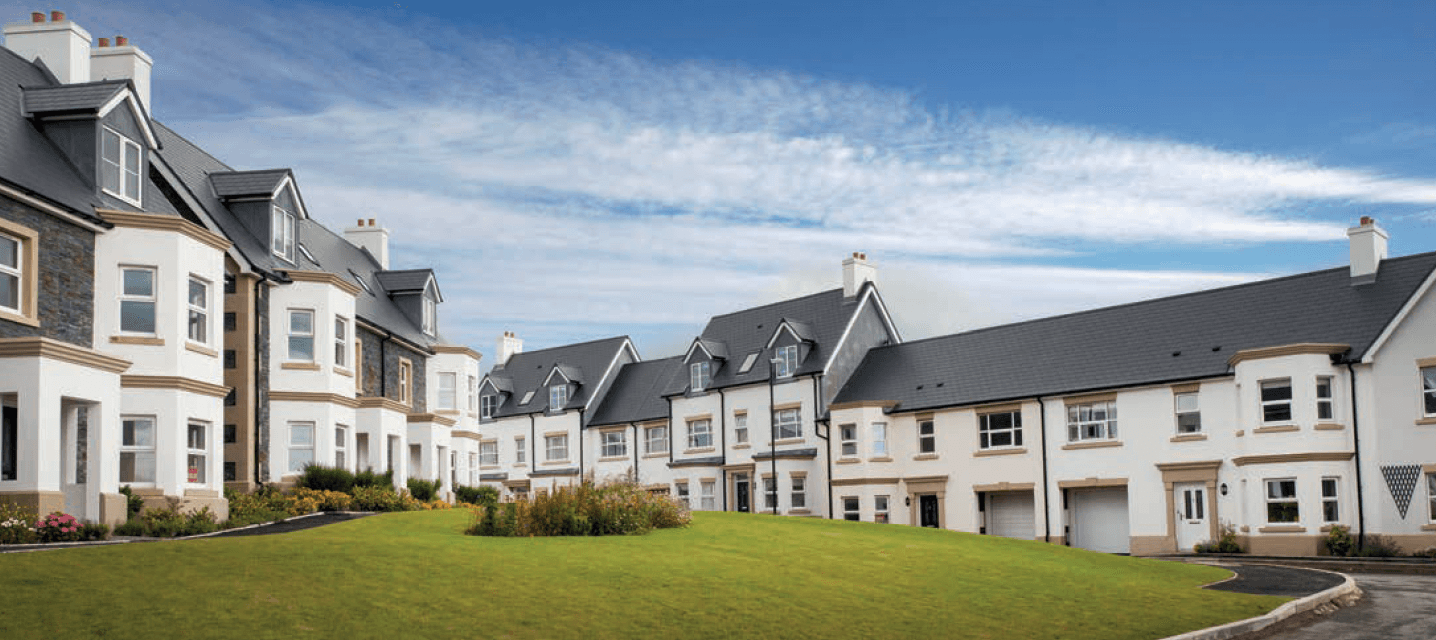
Future Homes Standard 2025: Transforming Roofing and Insulation
Explore how the Future Homes Standard 2025 is revolutionizing residential construction with new requirements for sustainable roofing and insulation solutions.
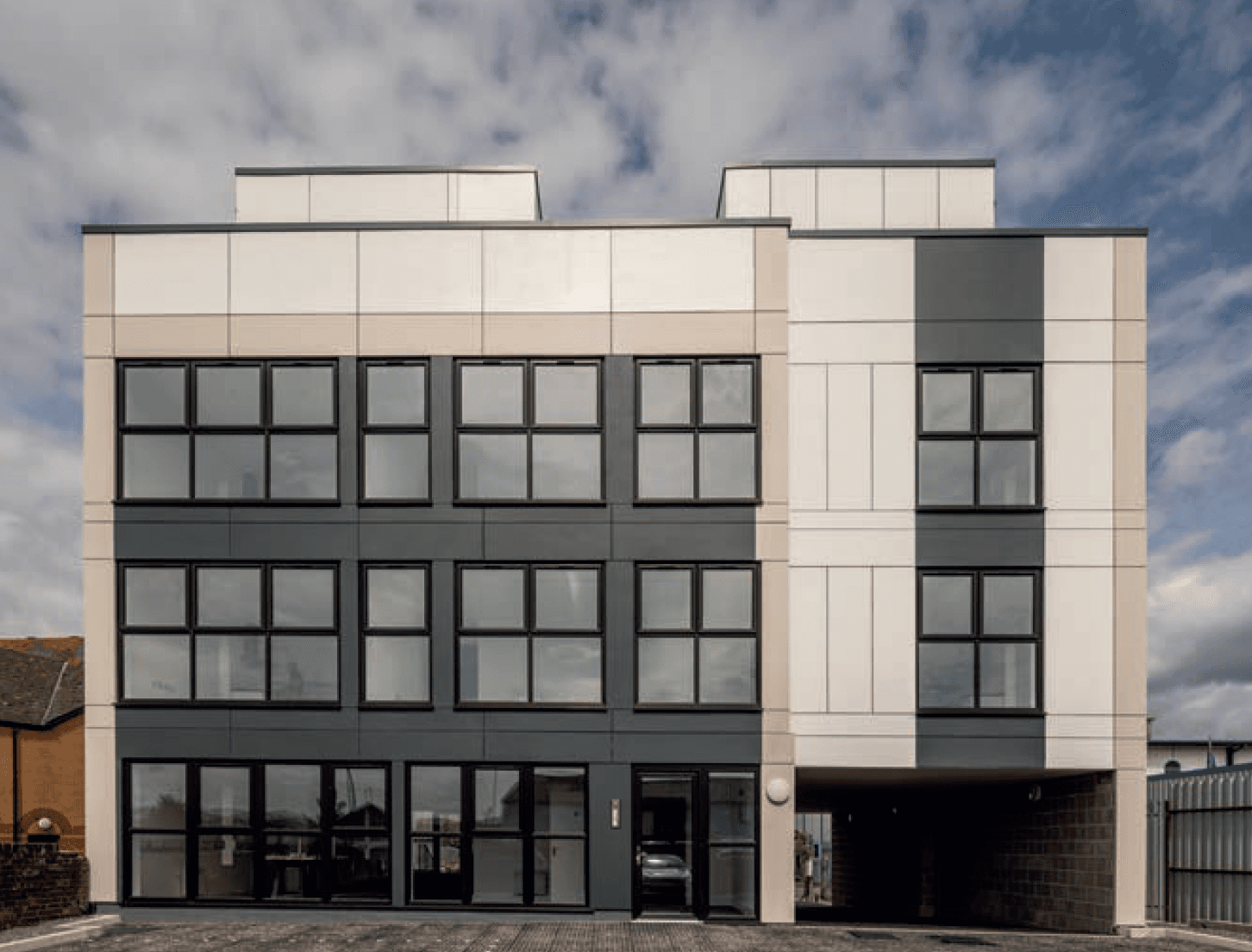
Hardie® Architectural Panel: Innovative Solution for Modular Construction
Discover how Beam Contracting utilized Hardie® Architectural Panel for their innovative modular flats project in Poole, delivering fire safety and sustainability benefits.